自动化系统
- 标准上下料装置
- 最新自动化线案例介绍
- 【钣金与制作】
2021年第4期版 - 【钣金与制作】
2020年第8期版 - 【钣金与制作】
2020年第4期版 - MWCS2019
钣金冲折自动化线 - 【钣金与制作】
2019年8月版
- 【钣金与制作】
- 生产线事例
最新自动化线案例介绍
浅谈钣金冲、折柔性自动化单元的实用性
“制造是一种精神,制造是现实的劳动,制造是创新的支撑,制造更是一种文化! ”这是中国锻压协会张金秘书长在《钣金与制作》杂志中讲述的一段话。对笔者来说,这段对于“制造”的定义让我感同身受。20世纪初,我有幸留学于制造立国的日本,大学毕业后在村田机械株式会社(以下简称“村田”)的钣金技术部门工作,并一直服务于国内外的客户。这段关于制造的定义提醒着我们,要不断提升自身企业素质和专业技术,实现钣金行业的“智”造。在工作期间,我接触过不少日本钣金公司,并与很多国内外客户一起设计探讨过柔性化钣金加工线,也做过多例村田独有的钣金柔性自动化案例。很荣幸能在这里与大家一起分享我的经验。
钣金冲、折柔性自动化加工线
接下来与大家一起分享的是两年前村田与上海某国际知名电梯公司一起研讨制作的钣金冲、折柔性自动化加工线(图1)。此加工线方案曾与该公司钣金工艺资深老前辈胡厂长一起探讨研究过,现已经陆续被配电柜、电梯、办公家具等多行业客户采用。
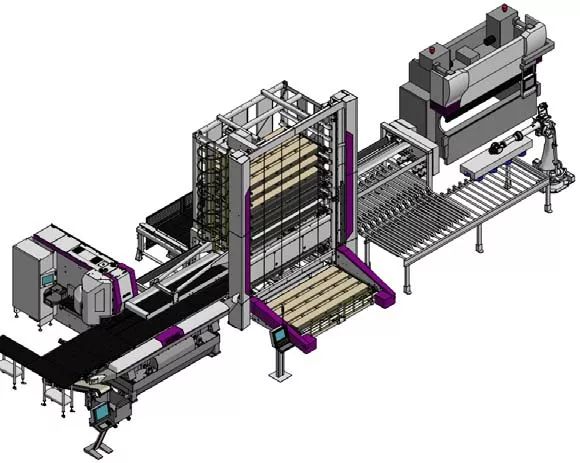
图1 村田机械独自设计的第1条冲、折柔性化加工线
当时某些厂家正在提供比较昂贵但柔性化不高的冲剪折加工线,但村田却采用标准数控冲床与数控折弯来进行了简单的集成,实现了一套全新标准的自动柔性化冲、折生产线。此生产线可根据各行各业的需求,配合客户的实际生产进行简单的自由组合,从而提高了生产效率,减少了初期投资成本。譬如,当数控冲床的加工节拍时间比折弯机加工节拍时间快1倍时,可以采用1台冲床对2台折弯机的全自动联动线。
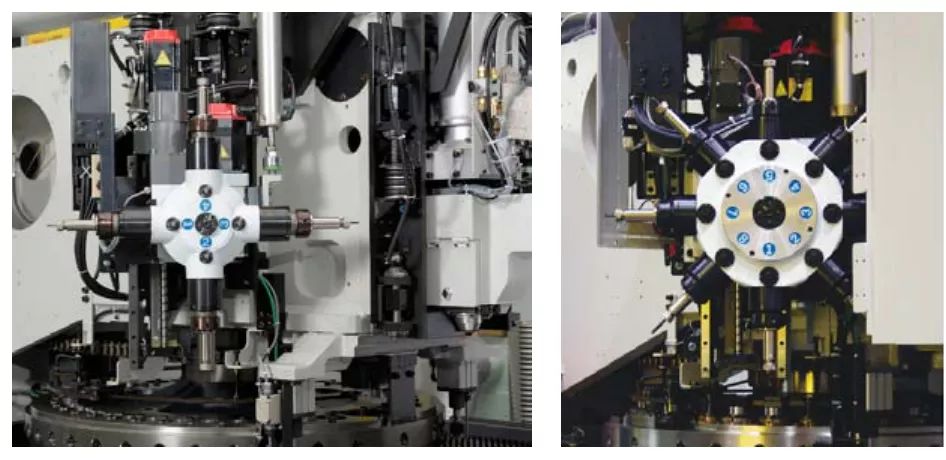
图2 纯伺服同步进给式4轴(左)和8轴(右)攻丝装置
采用高速数控来简化钣金加工工艺
村田的高速数控冲床M3048TG可不占用转塔工位,外挂纯伺服同步进给式4轴或8轴攻丝装置(图2)。可以加工M2~M10的攻丝,加工1个大概需要1秒多一点。根据客户的需求可选择切削式或锻压式的市贩丝锥。在1台冲床上确保加工精度的前提下,省略2次定位搬送及2次攻丝的加工工序,实现冲孔翻边成形攻丝加工一体加工。其最大优势在于无需购买专用攻丝模具,只需采用一般的丝锥;无需2次人工干预、简化工艺流程。从而实现减少维护成本、运行人工及专业攻丝装置的占地空间。毛边毛刺是钣金加工的天敌。采用专用去毛刺装置一般需要人工进行2次工序搬送、收集、码垛。一般专用去毛刺装置只能对板材全面去毛刺加工,会对材料表面造成划痕划伤。村田的专用去毛刺模具是本公司的专利技术,可以根据客户的需求对加工钣金零部件的指定部位进行去毛刺加工。在冲床上1次完成,并只需配1套去毛刺模具(图3),精简了复杂的钣金加工工艺。上述介绍的工艺方案是列举了两个在数控冲床上实现的钣金加工工艺集约精简的事例。
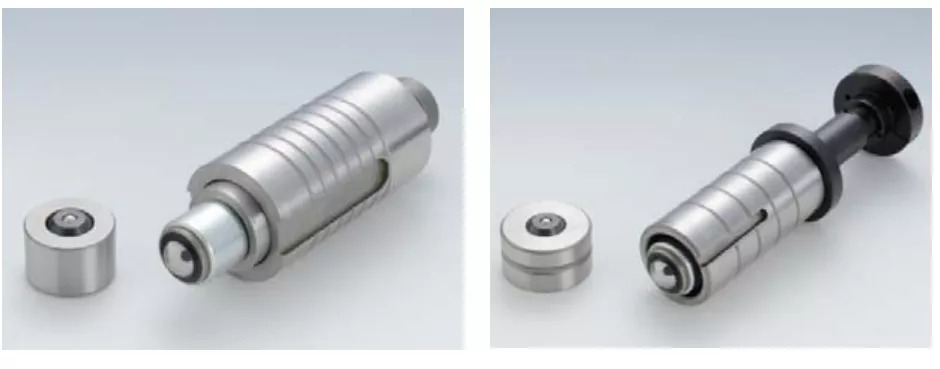
图3 村田专利去毛刺模具
钣金冲、折柔性自动化单元实用性
此次介绍的钣金冲、折柔性自动化单元装置的主要特征如下:⑴ 对使用定尺材加工,无需进行任何中间环节处理,可简单实现冲压、折弯一体自动化。⑵ 某些厂家的设备加工定尺材时,需要对定尺材进行修边加工。采用村田的冲床加工,则不需要此环节。直接节省了材料及加工时间,并提高了加工效率。⑶ 可以根据客户的加工产品形态,对数控冲床及折弯机的规格及吨位进行自由选配组合,来降低加工单元的初期投资成本。⑷ 可以根据客户的生产模式对此加工线单元进行自由组合。数控冲床+上下料库单元与折弯机+折弯机器人单元可各自作为独立单元进行自动化加工。而数控冲床作为单体也可进行手工上下料加工。⑸ 占地面积小,产品流向自由。生产线可从左至右或从右至左。根据客户需要可开放与后工序铆接、焊接、AGV等对接接口。
钣金冲、折柔性自动化单元系统运用说明
冲、折全自动运行模式
(与折弯机器人单元联线运行模式) 要进行冲、折联动加工运行时,如图4所示冲床上下料单元与折弯机器人单元构成全自动运行模式。上料装置从立体料库的上料区取出一张将要加工的板材 定位加工完了后 由延长下料装置进行下料搬送至折弯传送带上与机器人之间进行自动折弯联线。冲床、自动上下料立体料库、折弯机器人(下料机器人)及折弯机之间进行紧密的通信对接实现无中间环节的全自动的冲、折联动加工。
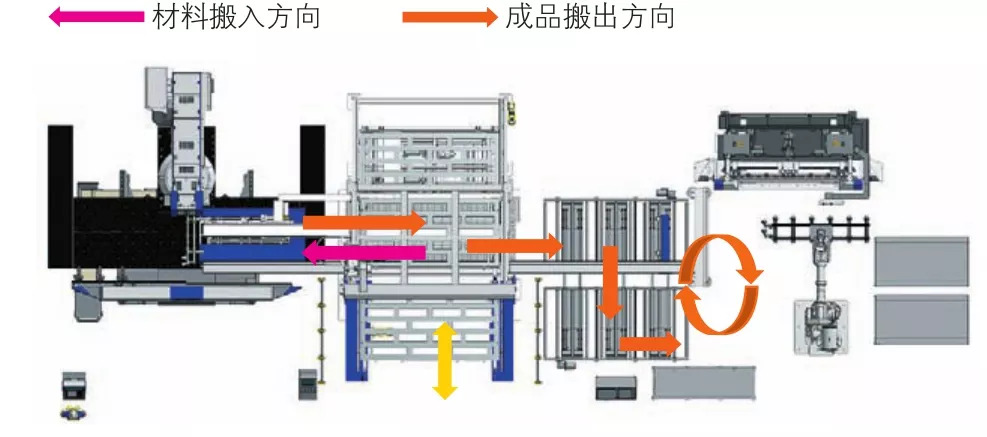
图4 冲、折全自动运行模式(与折弯机器人单元联动运行模式)
全自动运行模式(冲床上下料单元运行模式)
不需要与折弯机器人单元之间进行联动运行或夜间进行冲床单元无人自动加工时,冲床与料库之间可构成一个独立自动上下料单元进行运行,见图5。根据人工在冲床上制订好的加工计划将所需板材放入立体料库中将其材料层和成品层设定好。材料层的材料全部加工完之后可作为成品层来堆垛装载成品、8层的料库最多可制订自动循环存放7层成品(图6)。
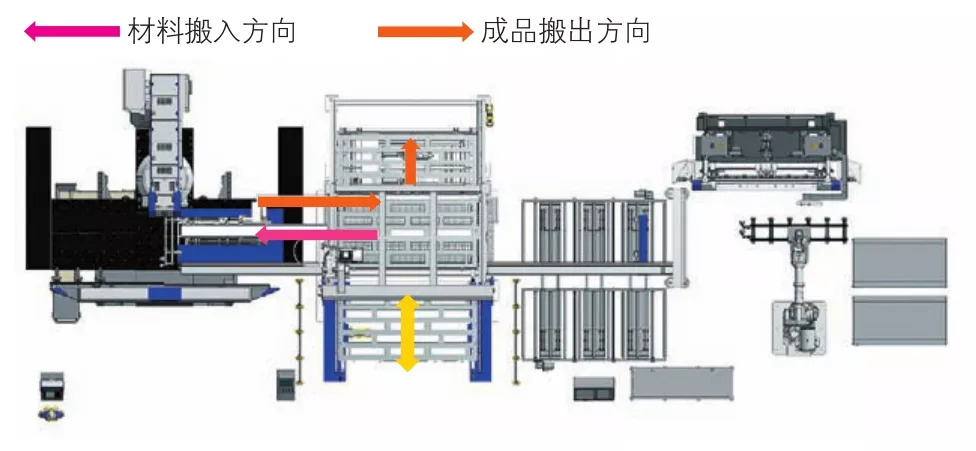
图5 全自动运行模式(冲床上下料单元运行模式)
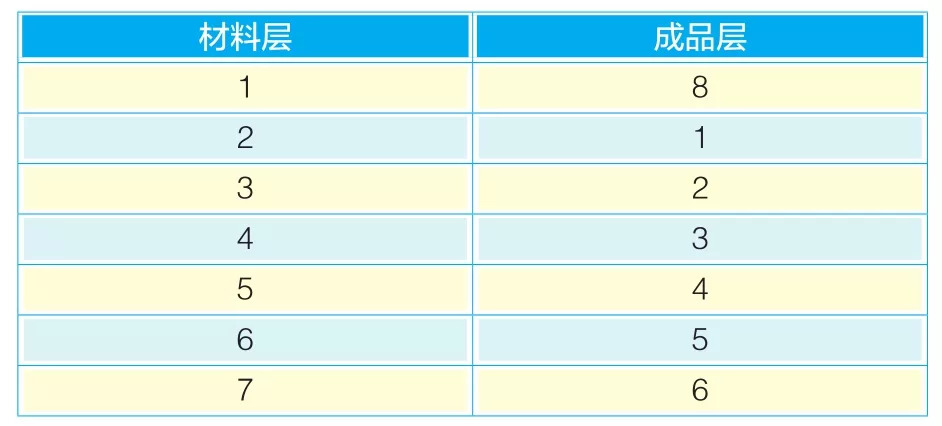
图6 加工计划材料、成品层设定例
自动运行模式(折弯机器人单元独立运行模式)
根据客户需要,折弯机器人单元也可以作为一个独立单元进行加工运行(图7)。如果冲床加工节拍时间与自动折弯节拍时间不相匹配,对其他冲床加工的工件需要自动折弯加工或联线冲床、料库发生故障等情况时,可采用此运行模式进行自动折弯加工。
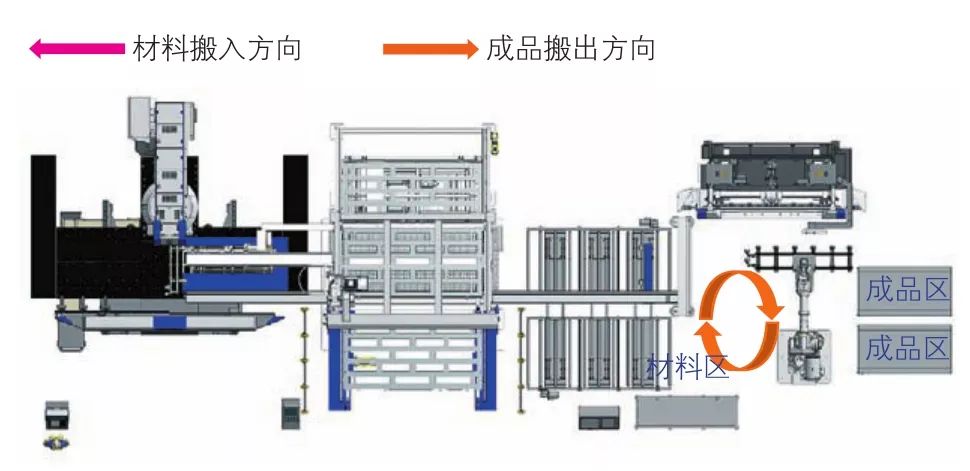
图7 自动运行模式(折弯机器人单元独立运行模式)
半自动运行模式(手动搬入→自动折弯运行模式)
少量需要紧急冲折加工时,可通过操作人员手动将加工板材进行手工上料、定位。冲床加工完了之后延长下料装置会将折弯工件自动搬送至折弯传送带上→传送带自动搬送至机器人吸料定位→与折弯机器人之间实现自动冲、折弯联动模式。
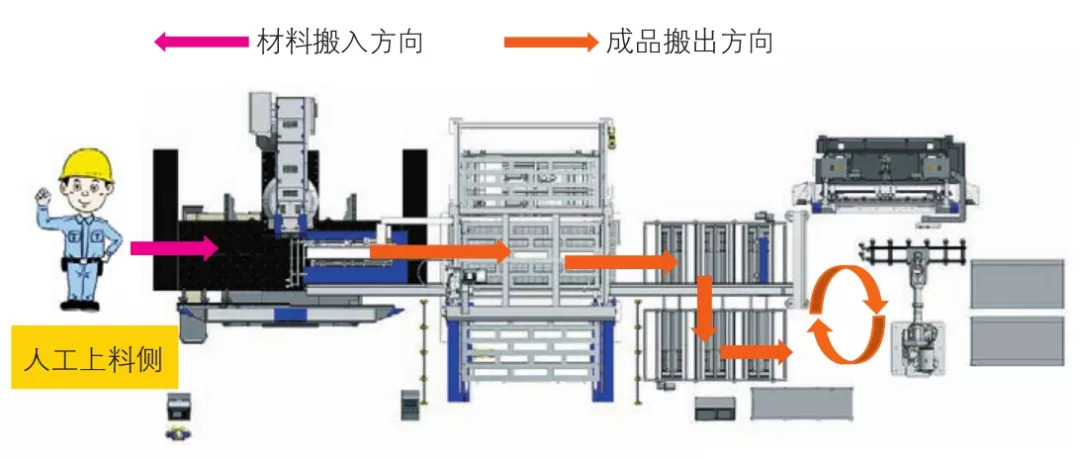
图8 半自动运行模式(手动搬入 自动折弯运行模式)
半自动运行模式(自动搬入→手动搬出模式)
出现对立体料库的材料进行紧急加工或大板套料加工后需要马上采用人工去微连接分拣等情况时,上料装置可以自动从立体料库的材料上料区吸取一张板材进行自动上料定位加工。由工作人员从冲床的左侧进行手动下料运行操作。
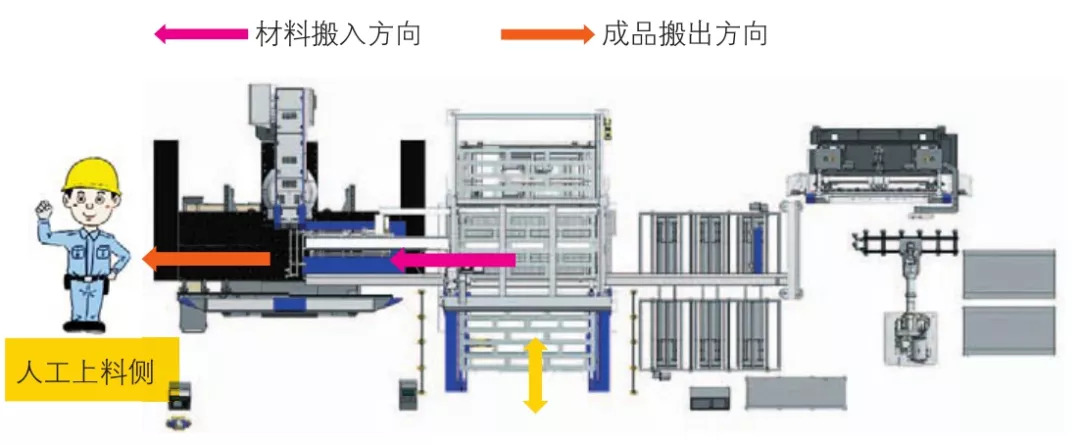
图9 半自动运行模式(自动搬入→手动搬出模式)
半自动运行模式(手动搬入→自动搬出模式)
工作人员一张张手动将加工材料定位上料之后加工开始,加工完了之后由立体料库的下料装置进行自动下料,将成品自动堆好垛后可手动出库或自动放进立体料库中。此模式适用于网孔板等加工。
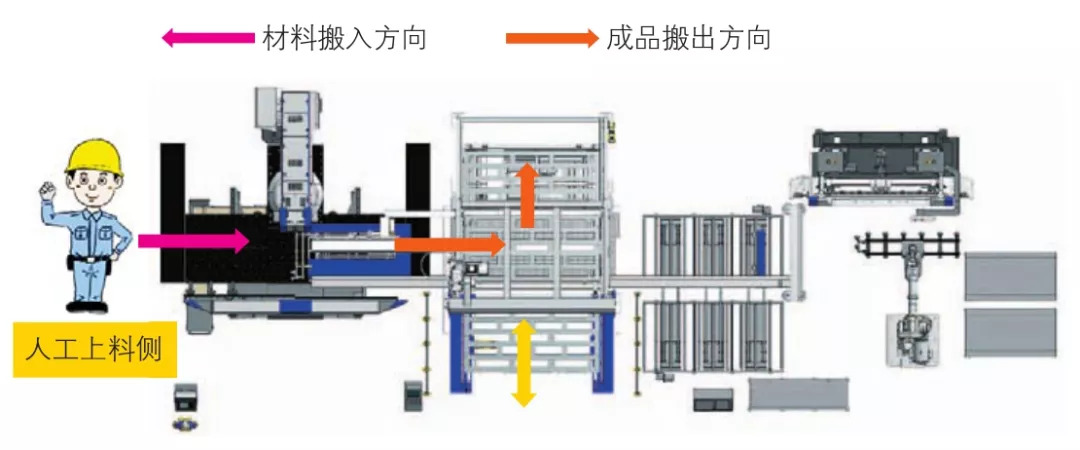
图10 半自动运行模式(手动搬 自动搬出模式)
冲床单体手动运行模式
立体料库单元故障或需要加急部品对应时,采用冲床单体手动运行模式。通过人工手动上下料来进行冲床单机加工以满足客户生产要求。冲床作为一个独立单元也可使用。
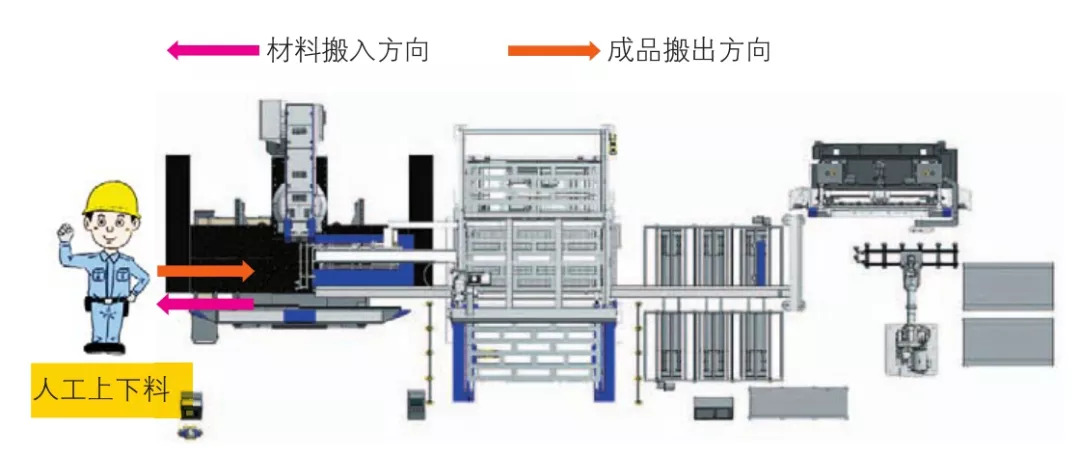
图11 冲床单体手动运行模式
折弯单体手动运行模式
折弯机器人自动折弯不可对应的工件,加急部品折弯工件等需要加工或折弯机器人发生故障时可采用折弯机单体模式。
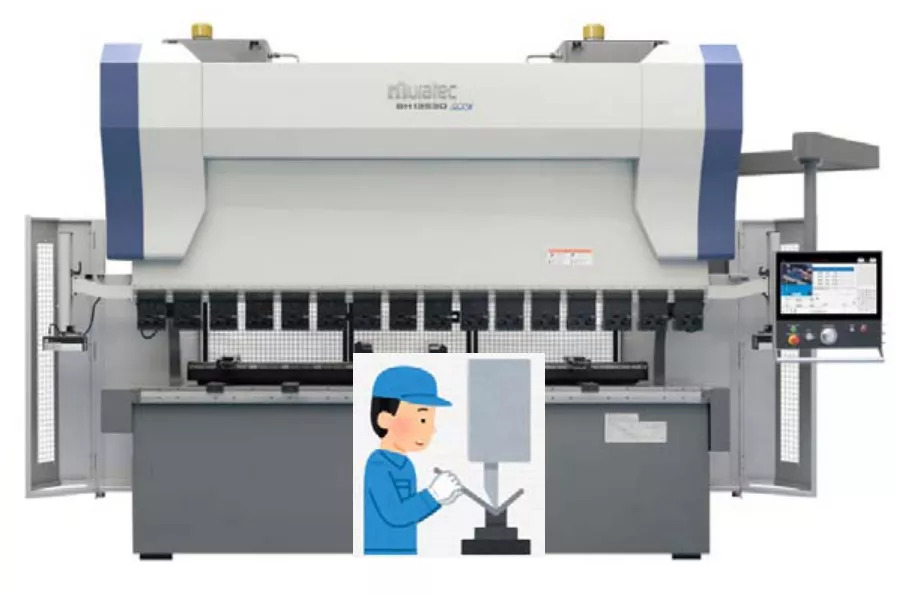
图12 折弯单体手动运行模式
结束语
随着国内劳动人口的减少,人工费用的上涨,对钣金自动化系统的要求会越来越多。从少种多量演变成多种少量的生产模式时,对自动化设备的柔性及通用性需求也不断升级,设备投资成本的回报更加重要。村田机械为应对各行各业客户的需求,采用主机进口设备与国产设备相结合,来解决客户的自动化变量生产及柔性化需求,并大幅度降低初期投资成本。希望此次介绍的“村田自动柔性化冲、折加工生产线”能给各位带来一些参考。
此冲·折自动软性化方案介绍在【钣金与制作】2019年8月版也同时登刊,详细请参考: